Du kan lave dine egne ski. Hvad ville du tænke, hvis du spurgte?
Sikkert ikke.
Det skyldes, at de eneste mennesker, der kan gøre det, er de perverse DIY-entusiaster eller nogle få topprofessionelle, der kan skabe signaturmodeller, og der er ingen fabrik, hvor alle kan gøre det.
Jeg har aldrig set sådan en service før. Hvis du havde den form og den ideelle vægt og den præstation, du havde forestillet dig i dit hoved, hvordan ville din glæde ved at stå på ski ændres? Jeg kan ikke stoppe med at være begejstret bare ved at forestille mig det.
Nå, det er alt, hvad jeg har hørt.
Det er fordi dagen er kommet, hvor du kan skabe din egen enestående ski med dine egne hænder.
Et sted, hvor du kan lave dit eget bræt
Et lille garagemærke i Minamiuonuma City, Niigata Prefecture gjorde det muligt.
SPÆNDING Design. Det ville være mere korrekt at sige, at det var et garagemærke. De plejede at være et ski- og snowboardmærke med base i Minamiuonuma, men nu har de udviklet deres eget udstyr og blevet en "producent", der laver originale boards.
Mr. Nagai, som er repræsentant for producenten og er bjergguide, tænkte på det i de felter, der dukker op hver dag.
"Hver dag bliver sjovere, hvis du kan skate på dit eget bræt."
Udviklingen af de originale ski og snowboards begyndte i juni 2021. Det er lidt over et år siden. Derfra, gennem gentagne forsøg og fejl, mestrede han hurtigt teknikken, og før ankomsten af sidste vinter, var han i stand til at lave en original ski som prototype. I dag har teknologien udviklet sig yderligere, og den er kommet til et punkt, hvor den er perfekt i forhold til grafik, ydeevne og finish.
Nu har de startet en service til at lave originale ski til almindelige brugere.
Dette inkluderer ikke kun muligheden for at skabe dine egne ski, men også "oplevelsesværdien" ved at se og arbejde på stedet, hvor skiene rent faktisk er lavet. At kunne se skifremstillingsstedet er en unik og værdifuld oplevelse.
Nå, med det in mente gik redaktionen faktisk ud for at lave en helt original ski.
Lad os tage et kig på hele processen denne gang.
Forberedelse af tavlematerialet
Skiene lavet af Voltage Design kaldes sandwichkonstruktion. Med det i tankerne, lad os fortsætte.
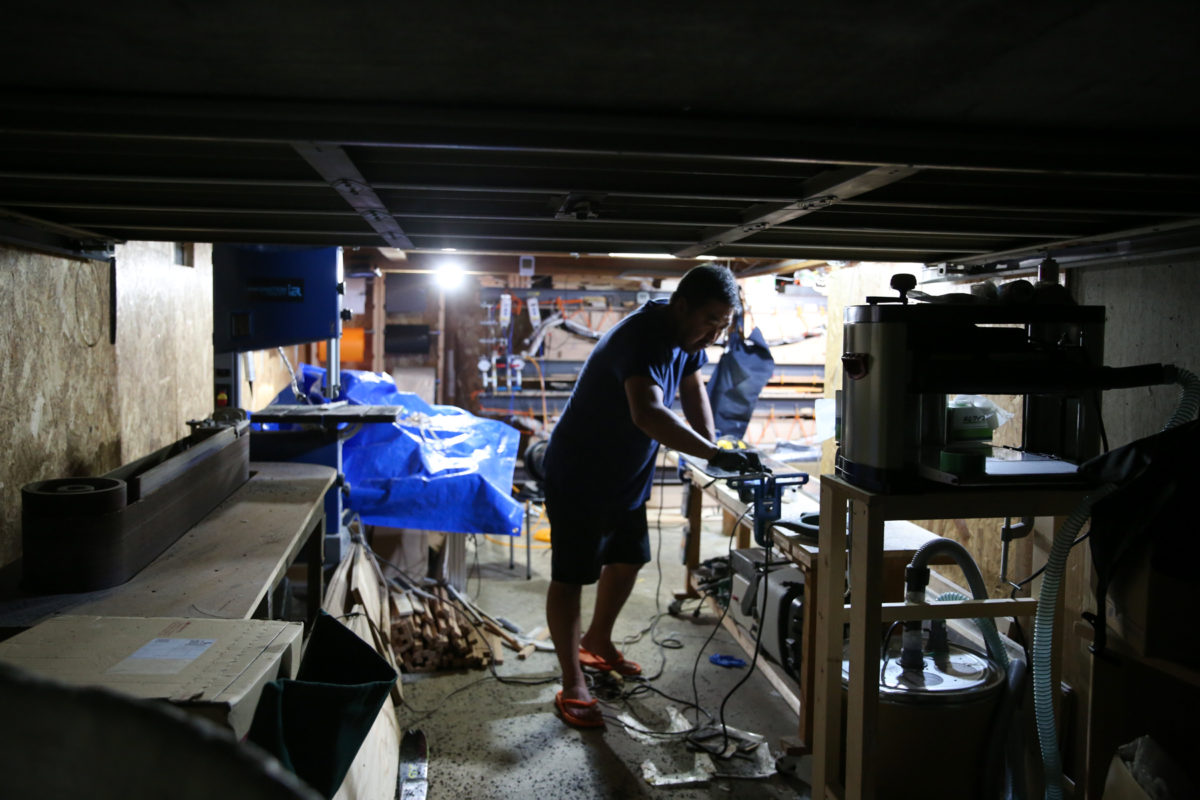
Først og fremmest er hovedmaterialet til ski træ. Ski er lavet ved at kombinere flere træsorter med forskellige egenskaber på det rigtige sted. Typerne er poppel, cypres og bambus.
En plade lavet af denne kombination kaldes et kernemateriale eller en kerne. Den rolle, som dette kernemateriale spiller, påvirker skiens hårdhed, spændstighed og vægt og er en vigtig faktor for at bestemme kørekvaliteten.
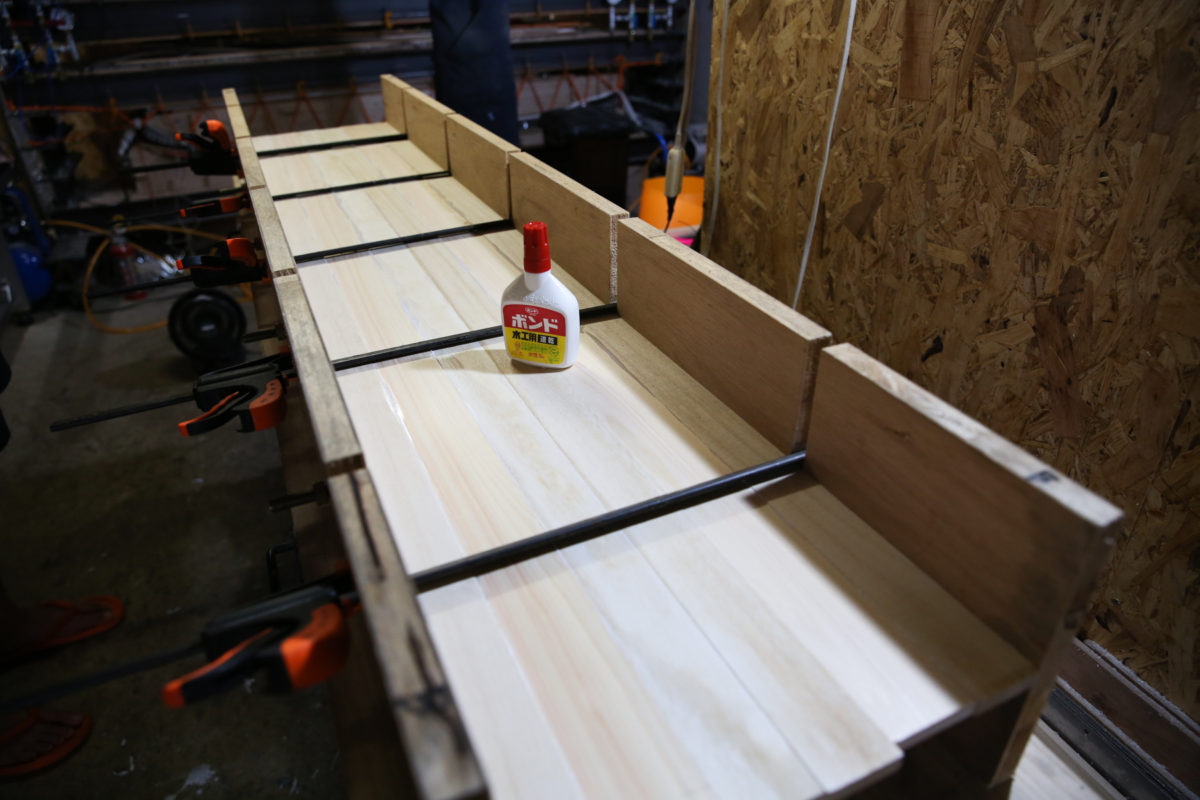
Bestyrelsen for spændingsdesignet bruger hovedsageligt lokal cypres og bruger paulownia på begge sider.
Dette skyldes, at cypressen er moderat hård, og paulowniaens lethed blandes for at opnå den passende fasthed og lethed af brættet.
Som et valg kan du vælge om du vil vælge forskellige træsorter, men mærket holder sig til disse to typer.
Det skyldes, at vi har besluttet at bruge materialer, der er produceret i præfekturet eller indenlandsk, når vi laver brædder. Dette har til formål at stimulere den indenlandske efterspørgsel og reducere CO2-emissioner fra transport.
Pladen er designet ved hjælp af designsoftware og CAD-software, indtil træet er limet sammen.
Denne gang vil jeg prøve at lave en skiform, som jeg aldrig har set før.
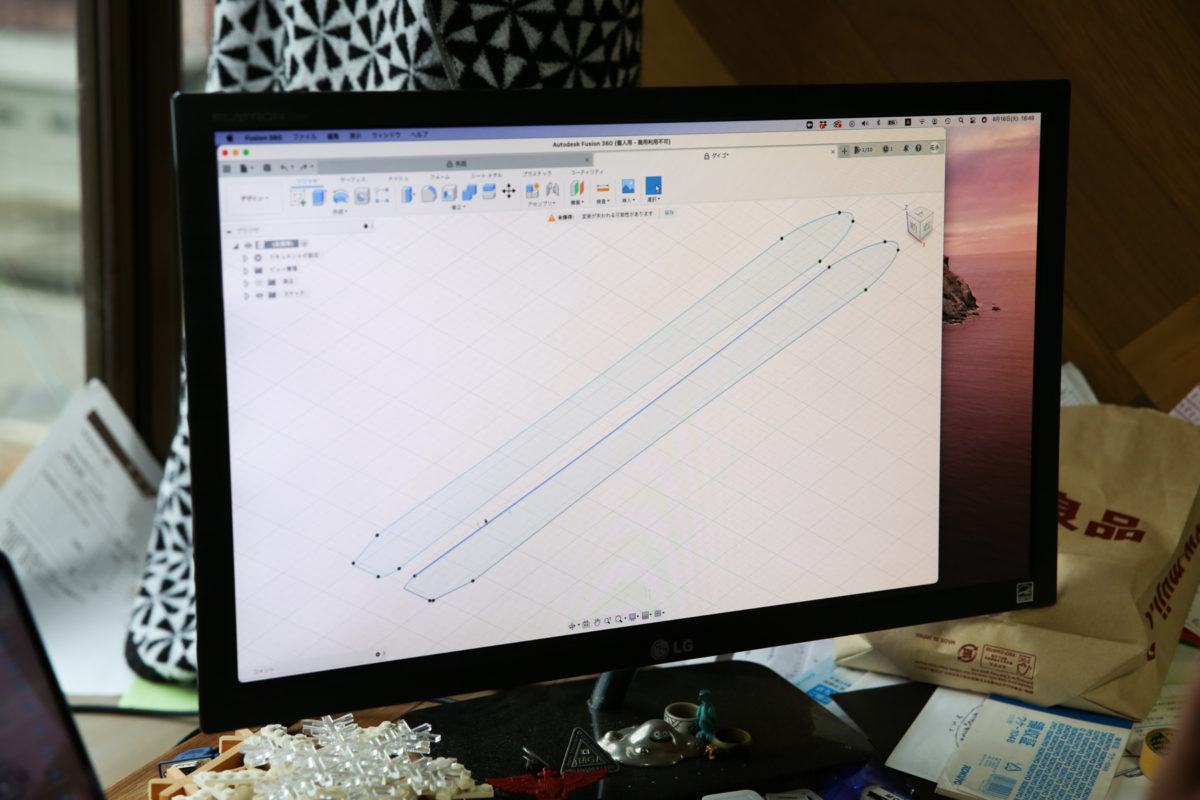
Sammenfattende er centerbredden 116 cm, næsen er 148 cm, halen er 137 cm, og den samlede længde er 178 cm. Jeg designede næsen til at være skarp (visuelt for min personlige æstetik) og den effektive kant af halen til at være længere på indersiden af brættet og kortere på ydersiden. Det skyldes, at jeg ønskede at kunne træde fast på kanten af dalfoden på tidspunktet for svinget, og forbedre betjeningsevnen med god kantfrigang på bjergfoden. Dette er fuldstændig eksperimentelt, og vi ved ikke, om det virker, før vi rent faktisk kører på det på sneklædte bjerge.
Når designet var færdigt, var det tid til at lime træet færdigt sammen. Da tykkelsen af den laminerede kerne varierer, bruges en automatisk høvl til at barbere den jævnt.
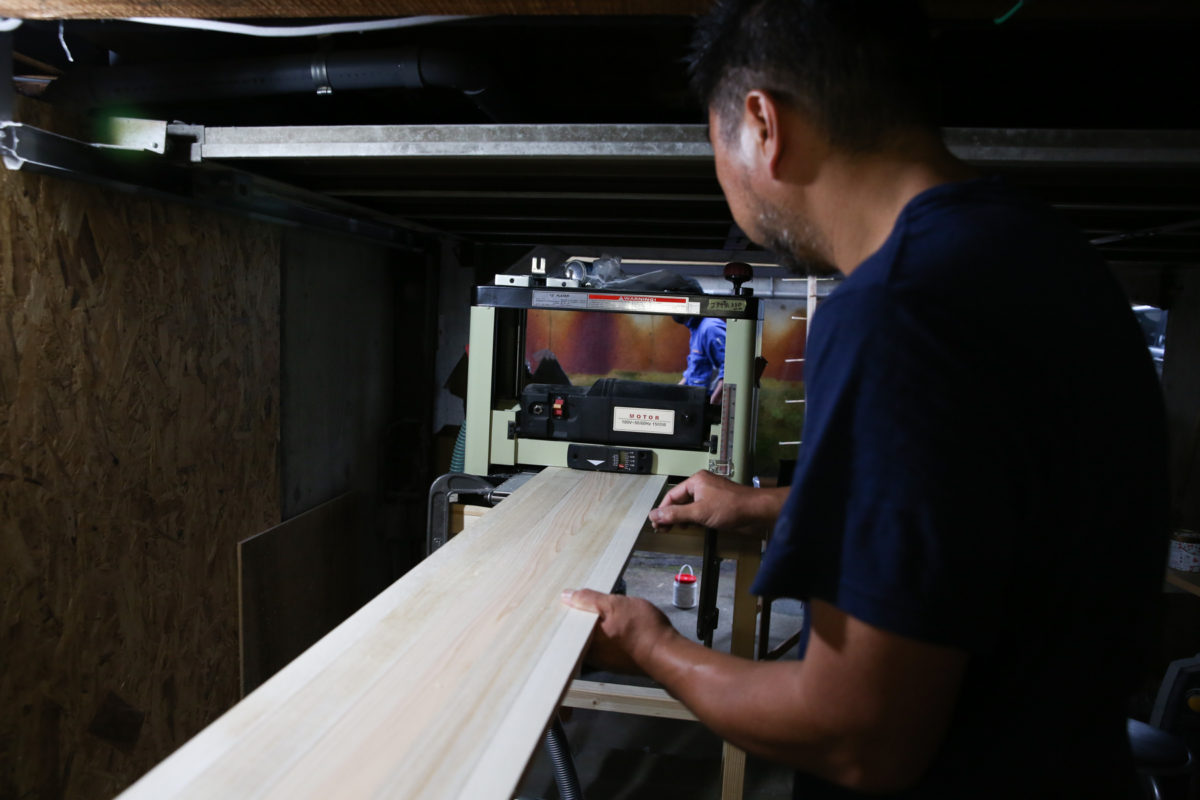
Når tykkelsen er ensartet, vil jeg bringe tegningsdataene ind i et nærliggende snedkerværksted og bede dem om at grave en rille på ydersiden i henhold til det design, jeg lige har lavet.
Derudover beder vi dem om at lave en skabelon, der vil fungere som standard for den tavle, de har designet. Efter denne skabelon dannes så sål, toplag, forstærkningsmaterialer osv., så selv materialer, der er forberedt separat, kan lægges oven på hinanden uden nogen afvigelser Vi laver støbeforme i stedet for skabeloner for at producere en stor mængde .
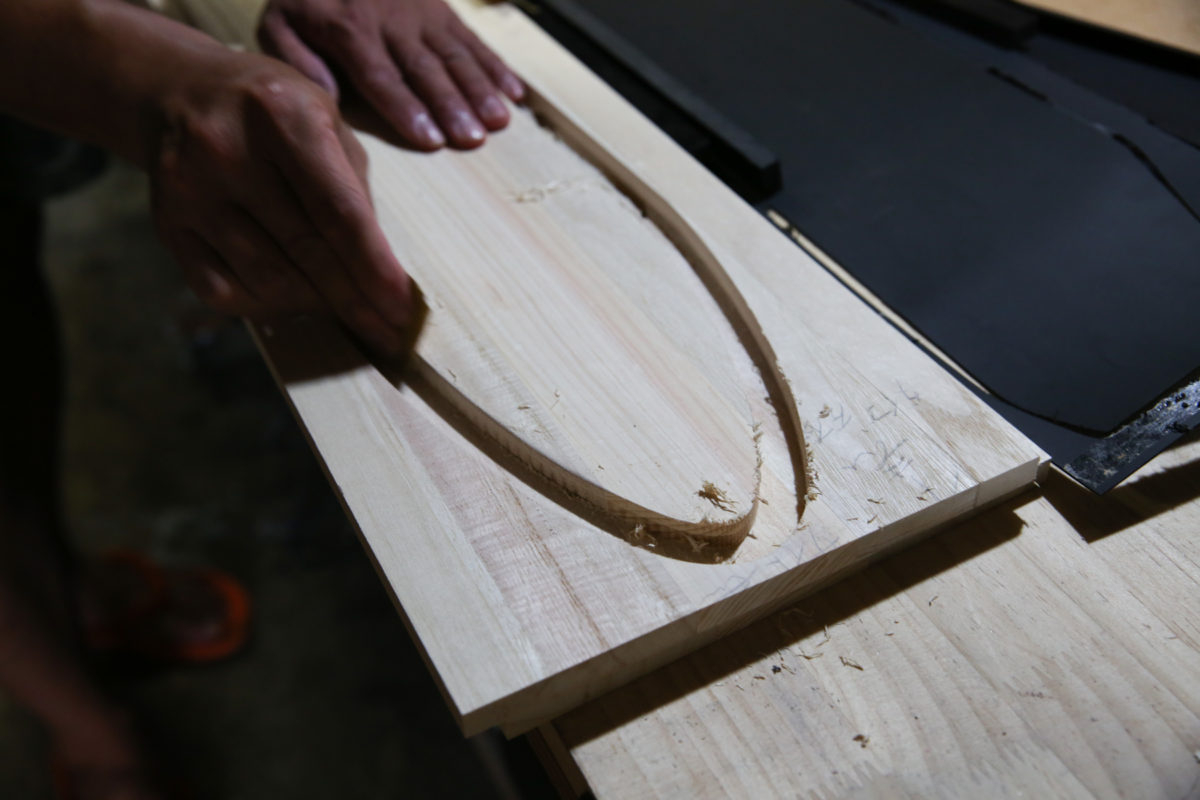
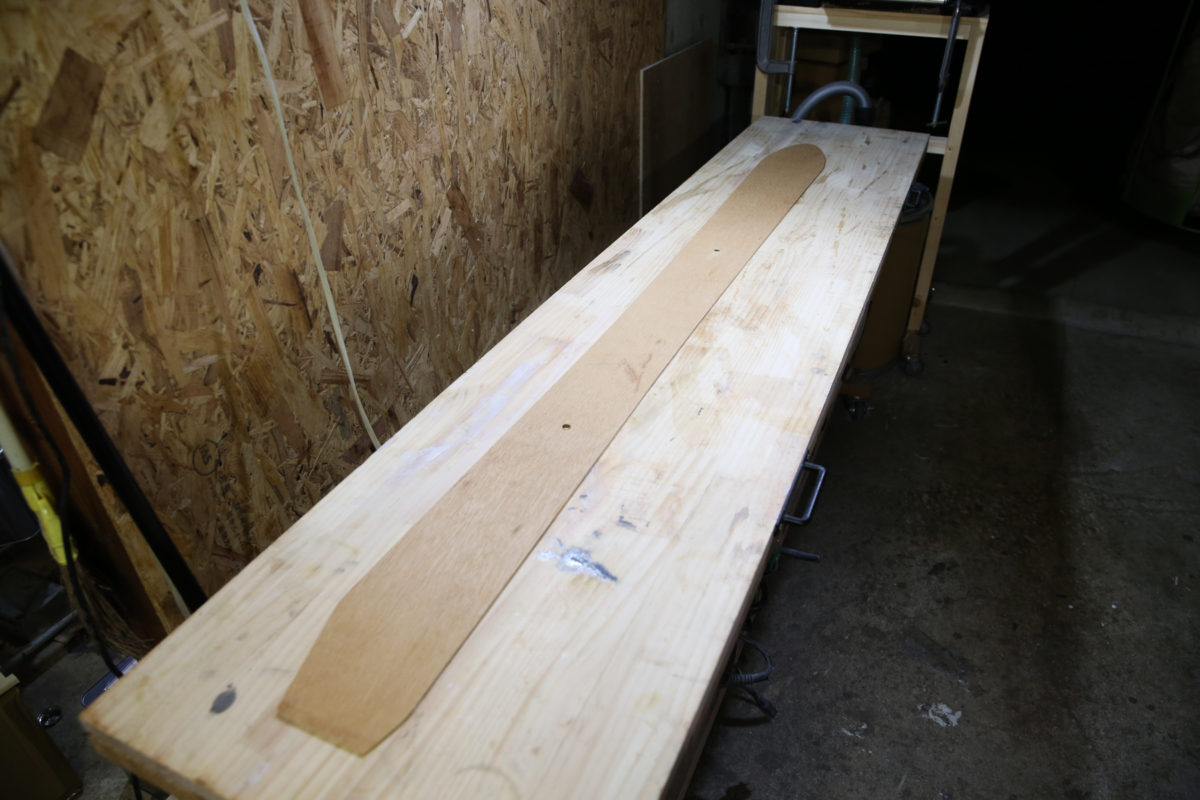
Sæt derefter ABS-harpiks og opskummet urethan i rillen lavet af snedkerværkstedet. Dette vil være din sidevæg. Sidevæggens rolle er at øge kantgrebet. Hvad angår denne ABS-harpiks, bruger næsten alle producenter lignende materialer, så der er ingen stor forskel. ABS-harpiksen lægges i cirka længden af den effektive kant, og spidsen af næse og hale indeholder urethanskum. Dette er for at lette behandlingen og reducere omkostningerne.
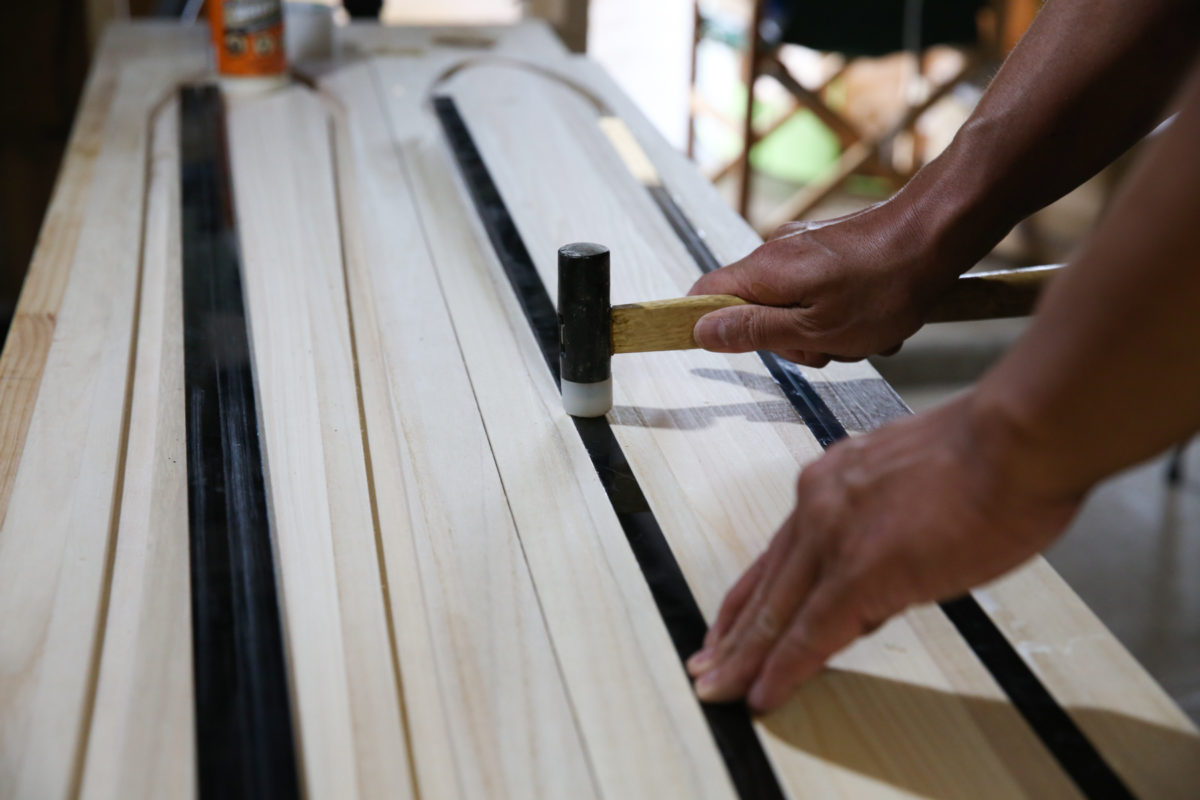

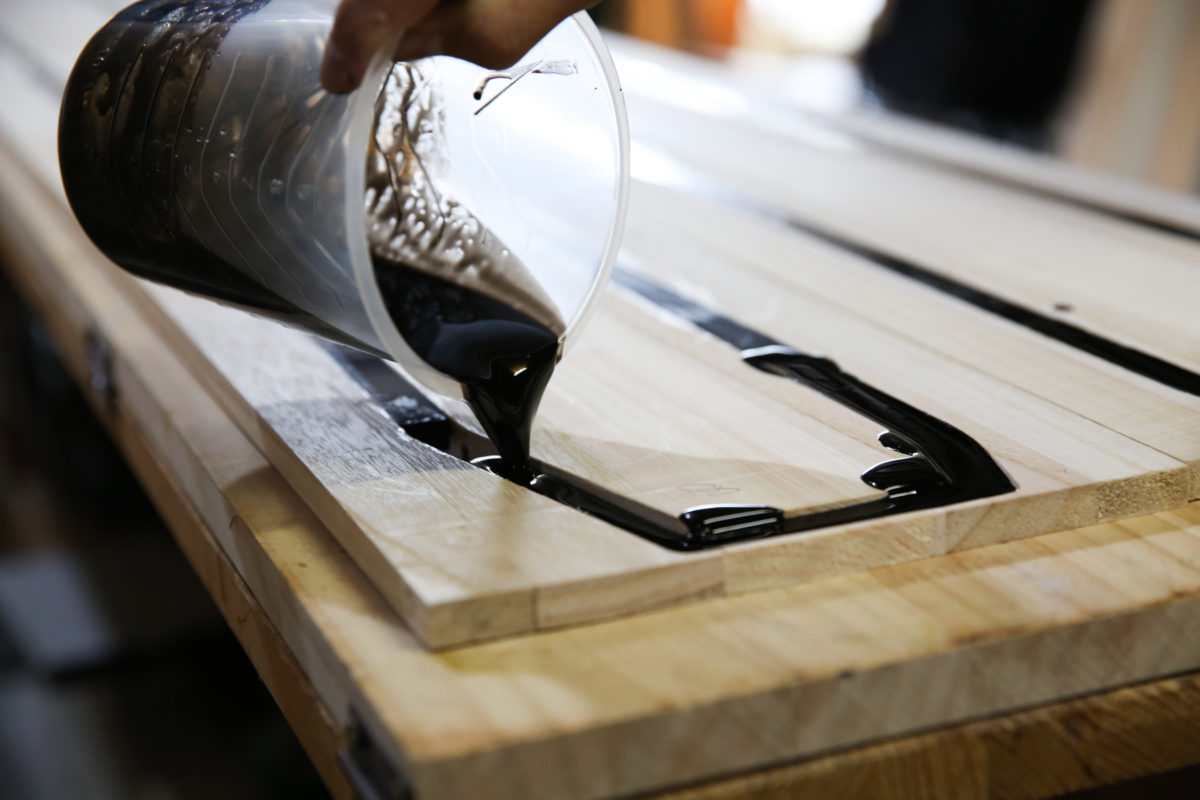
Gå videre til næste trin, indtil urethanskummet hærder. Det er et snit ud af sålen. Sålmaterialet er sintret sål med en molekylvægt på 40.000 indkøbt fra en indenlandsk fabrik. Kort sagt, jo højere tal, jo bedre glideydelse. Tallet på 40.000 er en stor kategori. Det er fordi jeg gerne vil lave noget med fremragende glideevne.
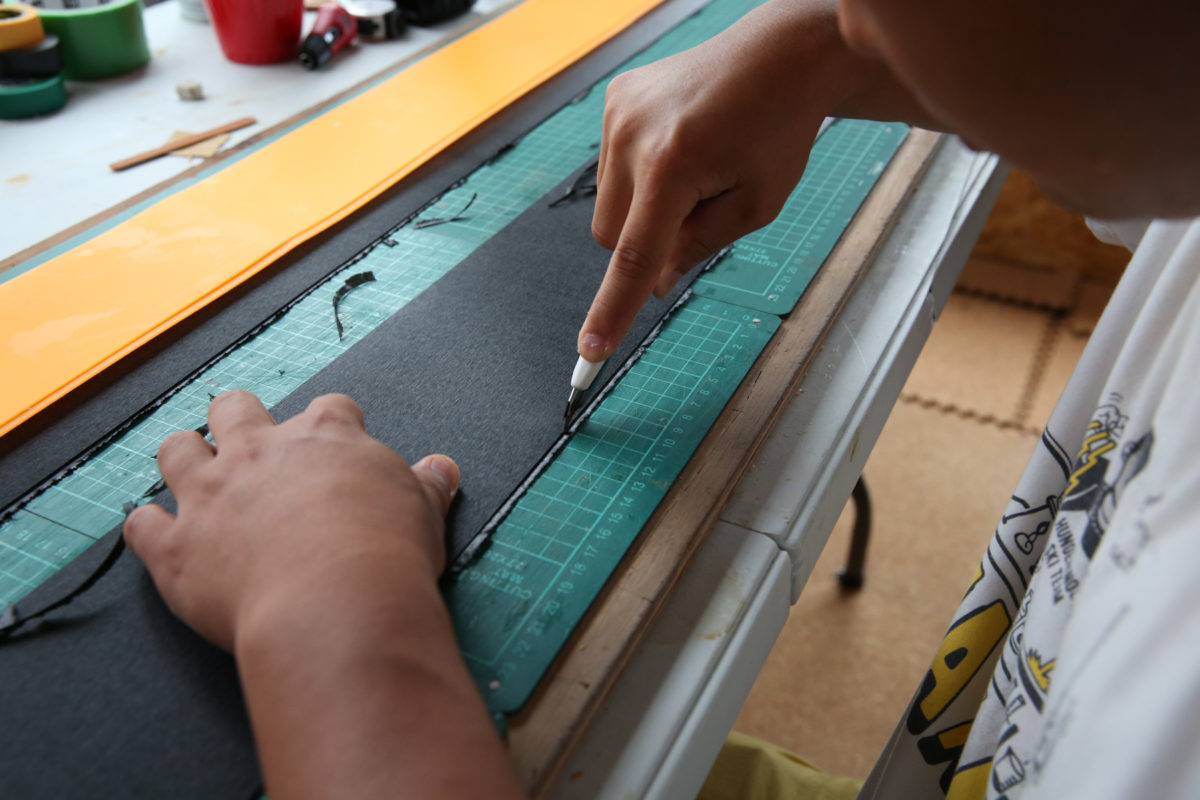
Når urethanskummet stivner, går jeg til fittingsbutikken igen. Her bruges en automatisk høvl, der kan styres i enheder af tiendedele af en millimeter, for at bringe brættets tykkelse tættere på den færdige tykkelse. Efter justering af tykkelsen, tynd kun næse og hale. Som du ved, er ski tykkere under fødderne og tyndere i næse og hale for bedre manøvredygtighed.
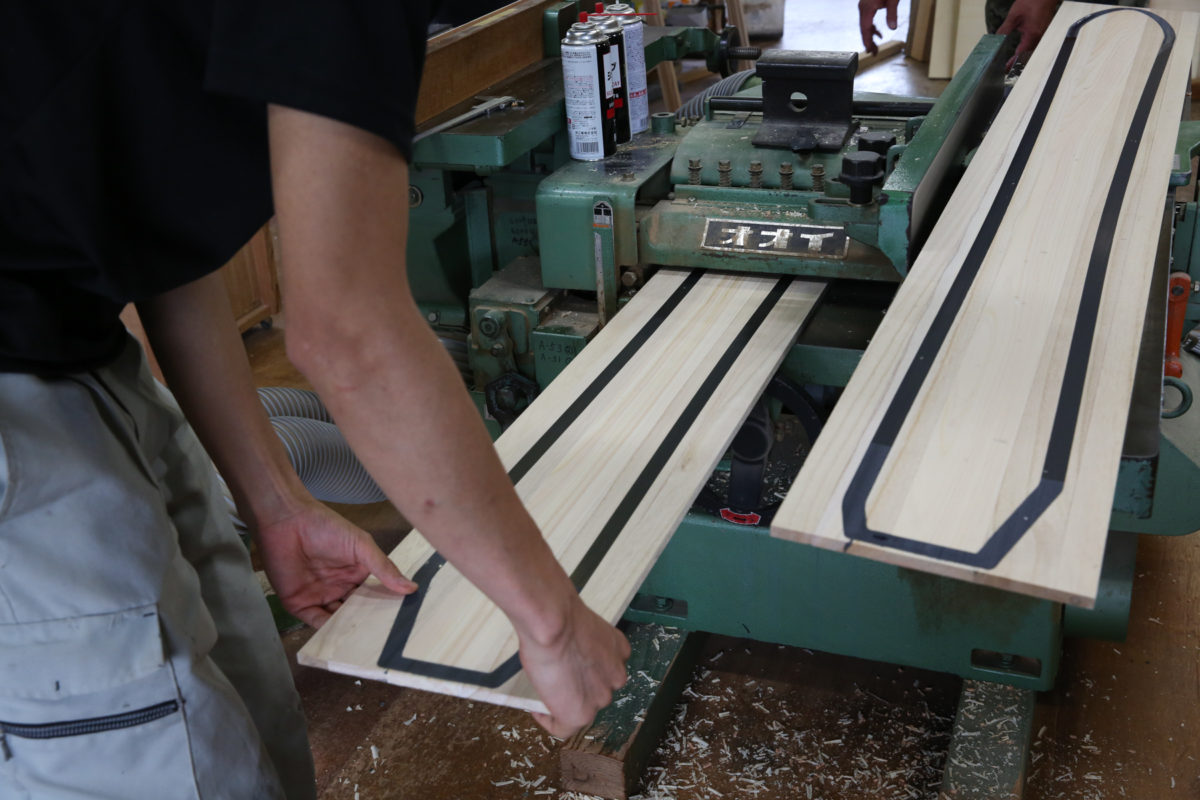
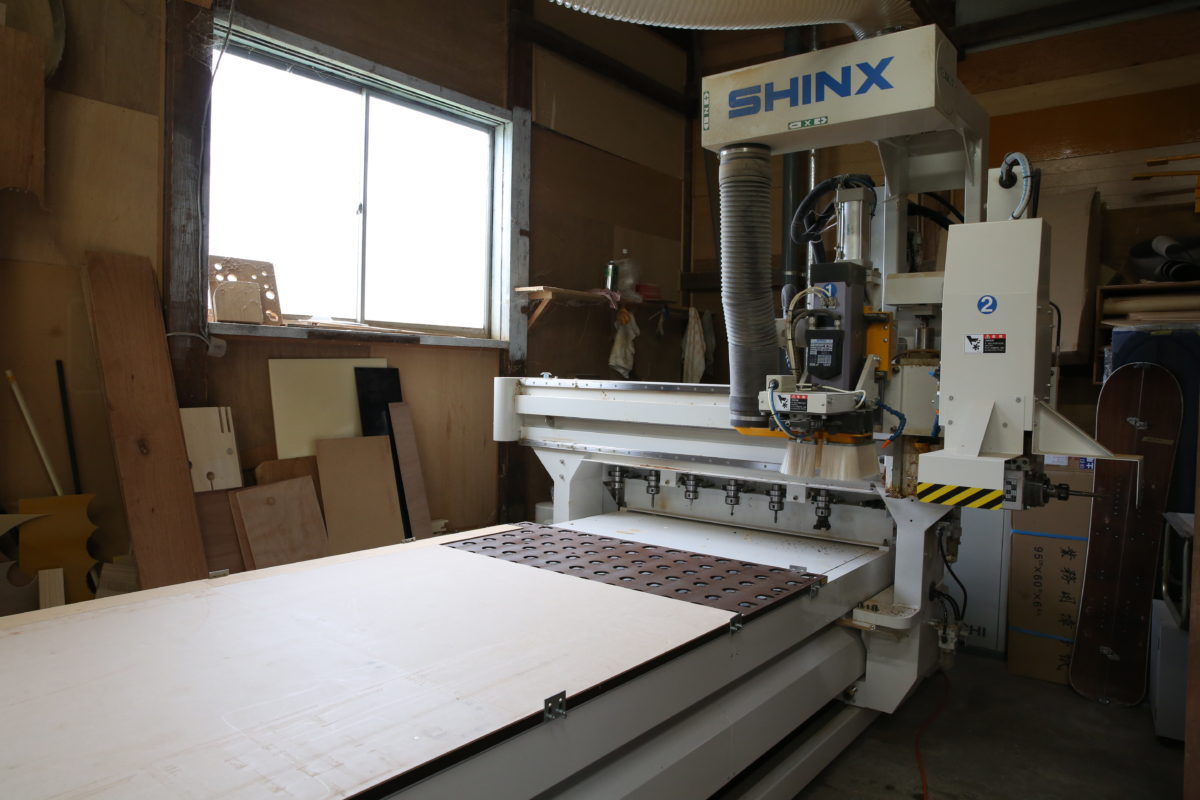
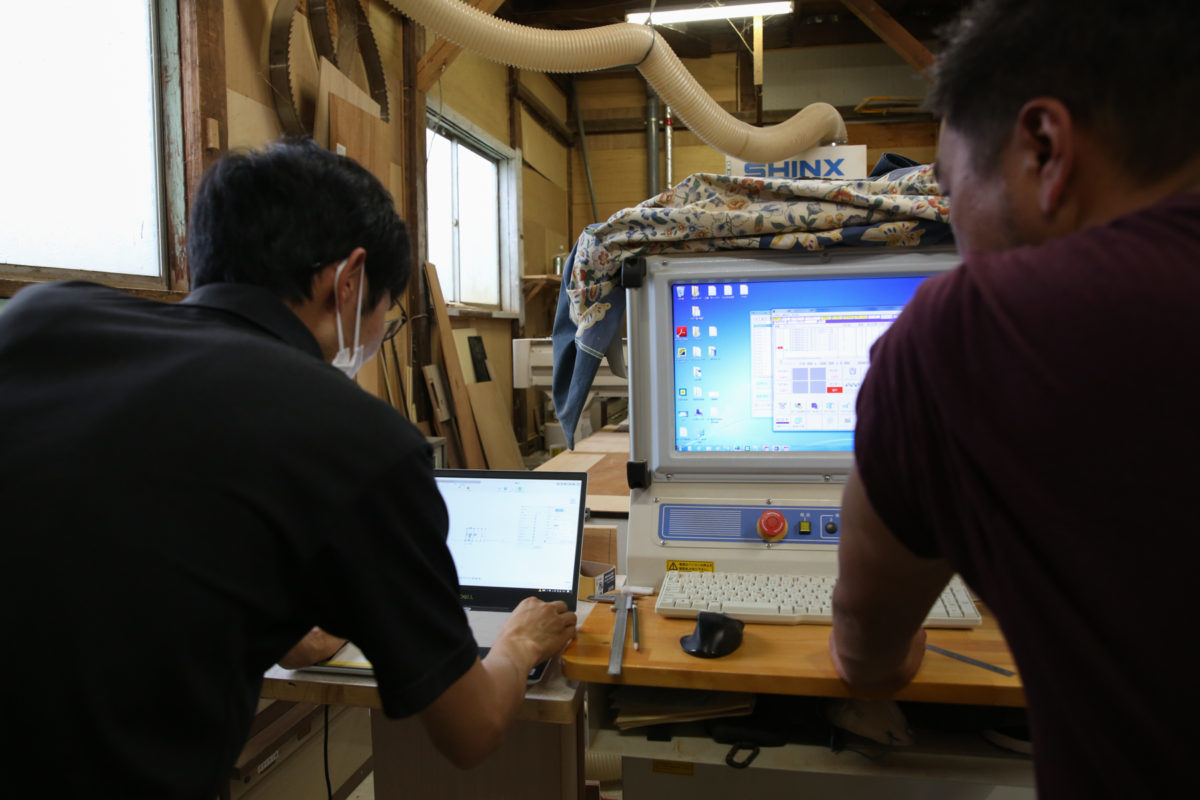
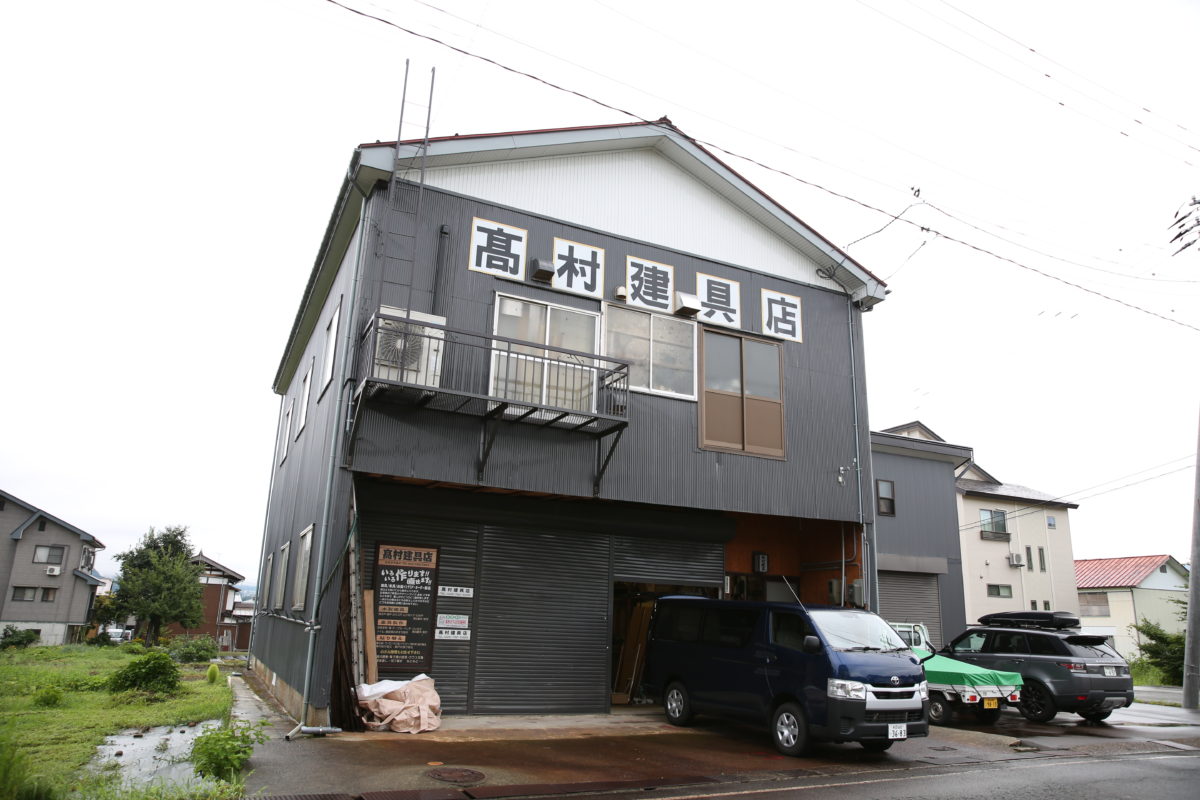
Gå derefter videre til kantbehandling. Kanten bruger en stålkant bestilt fra et kantfirma i Joetsu City, Niigata Prefecture. Den ene langkant bøjes i hånden. Det er sværere end det ser ud til at bøje langs brættets subtile kurve. Fuld wrap dette fra spidsen af næsen til spidsen af halen.
Efter at have forberedt kanten, design grafikken af brættet. Du er helt fri i denne henseende. Du kan bruge dine egne fotos eller tegninger, eller du kan ikke skrive noget. Du kan sætte dine yndlingsord på det, eller alt er fint. Lad os få den originale skifølelse frem til fulde.
Indtil videre har der været fokus på klargøring af materialerne, og fra næste side er det endelig slut med skifremstillingen.