Arbejde med at samle materialer
Herfra kombineres de alle på én gang og nærmer sig højdepunktet i skifremstilling.
Så jeg satte den bøjede kant på sålen og limede den sammen.
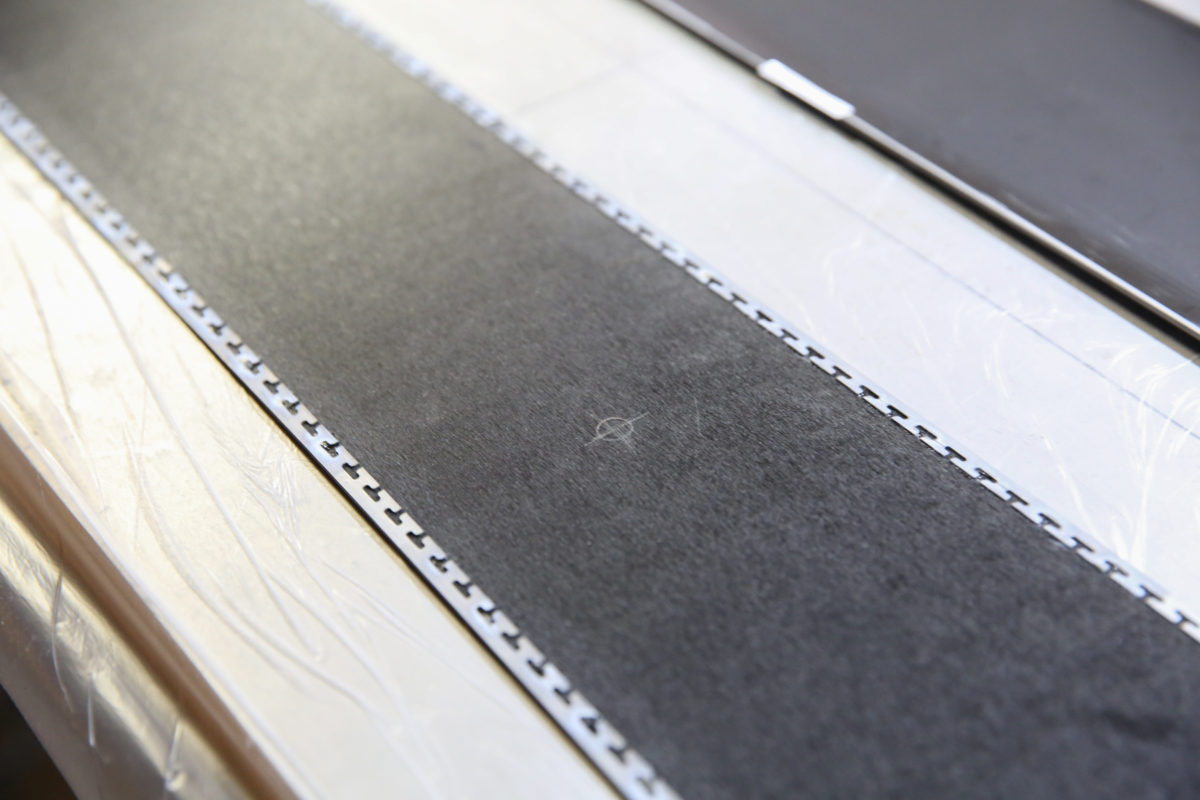
Påfør harpiks på toppen og lag glasfiber. Forresten betyder "harpiks" "epoxyharpiks". Mænd er ikke bekendt med det, men det bruges ofte til kvinders neglekunst. Harpiksen, der bruges denne gang, er en to-væske type, der blander hovedmidlet og hærderen. Dette vil klæbe og hærde over tid.
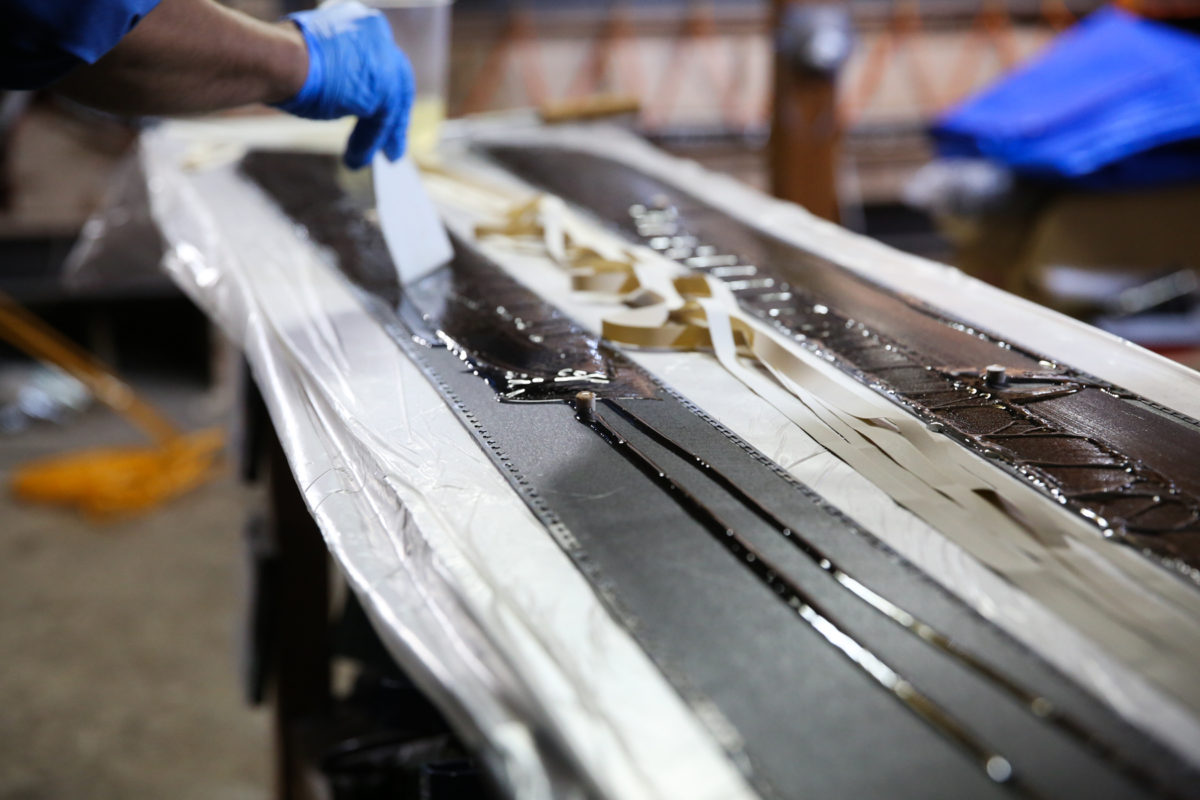
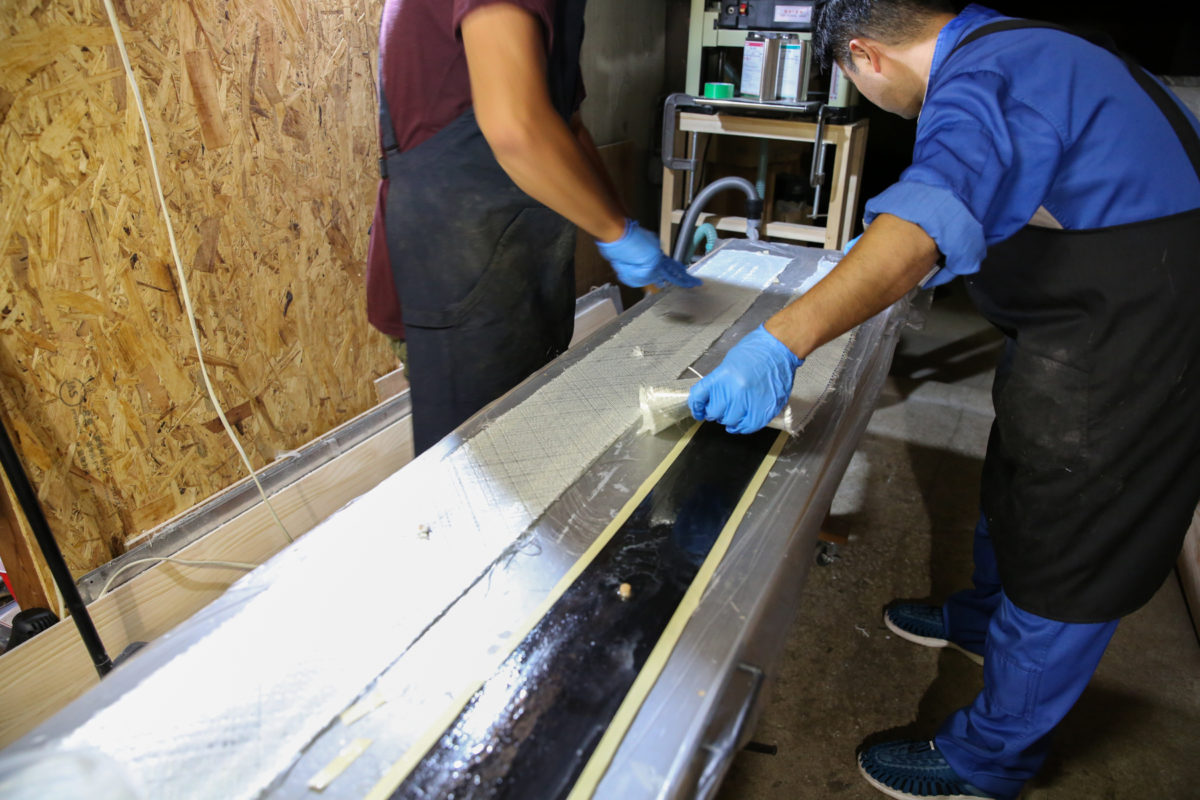
Efter jævnt påføring af harpiksen, lag kernematerialet ovenpå det. Påfør derefter mere harpiks. Læg glasfiber ovenpå og påfør harpiks. Denne operation kaldes laminering.
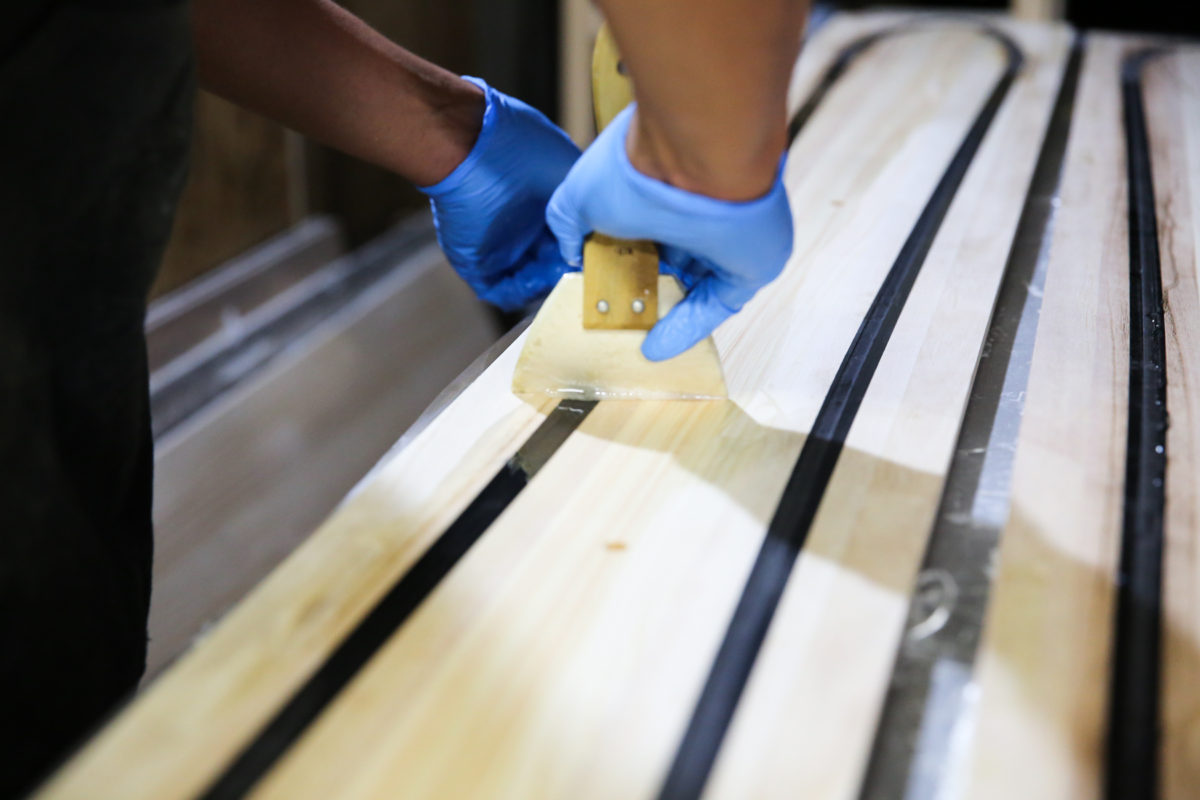
Forstærkende materialer såsom kulstof og titanal kan lægges i lag under denne glasfiberlagproces.
Fordelen ved sandwichstrukturen er, at den kan presses selv når der tilføjes forstærkningsmaterialer for at øge tykkelsen. Det betyder, at selvom du pakker mange ting ind i den, vil det stadig være en ski.
Ved at lave pladen denne gang ville jeg opleve træets naturlige fleksibilitet og hårdhed så meget som muligt, så jeg brugte kun glasfiber som forstærkningsmiddel. Indtil nu har jeg kun kørt på ski, der indeholder avancerede materialer, så jeg ville prøve et bræt, der var tæt på den naturlige kørefølelse af træ. Glasfiberen fungerer i øvrigt som en fjeder og skaber en passende mængde frastødning på brættet. Mærket sætter stort set to stykker over og under kernematerialet, men afhængigt af din præference behøver du ikke at lægge selv dette.
Når det andet lag af glasfiber er overlejret, skal du placere grafikken, du lige har printet, ovenpå og derefter lægge forsidearket over det.
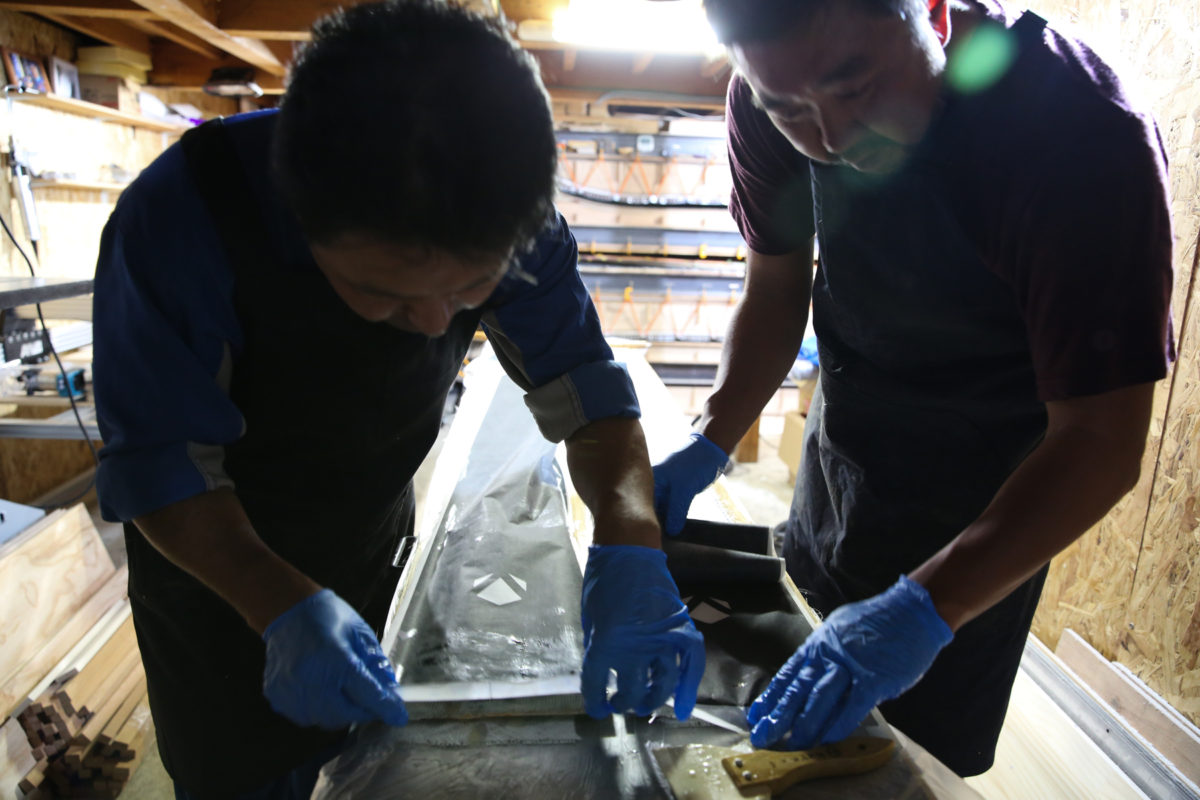
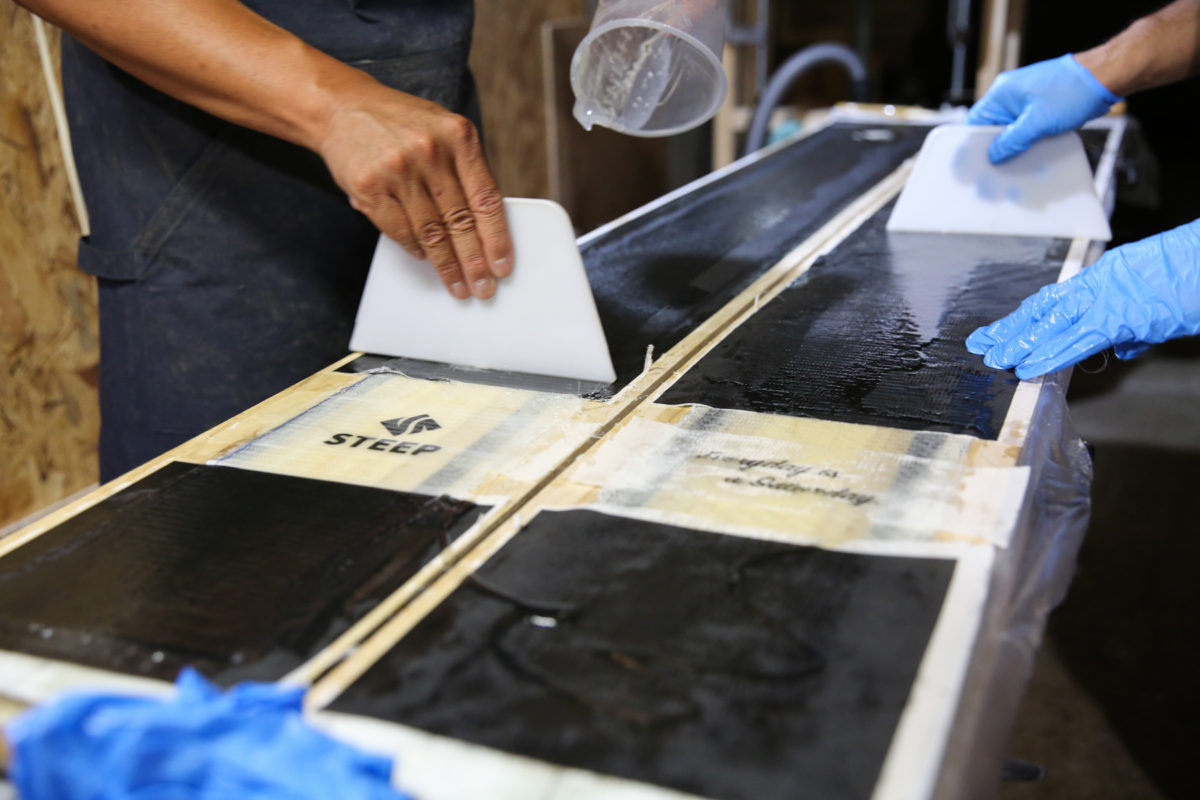
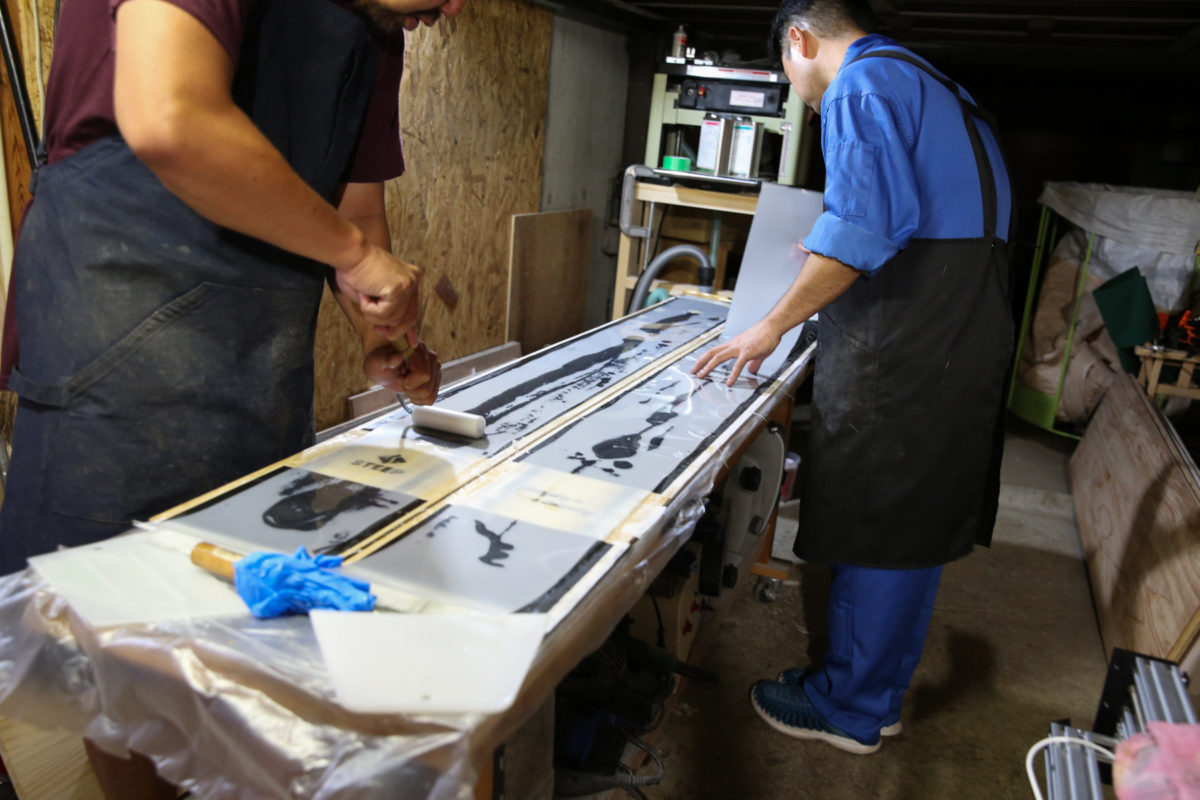
Forsidelaget har et stærkt beskyttelsesformål og har ikke en særlig funktionel rolle relateret til glideydelse.
Nu, når materialerne er lagt i lag, er det endelig tid til pressearbejdet.
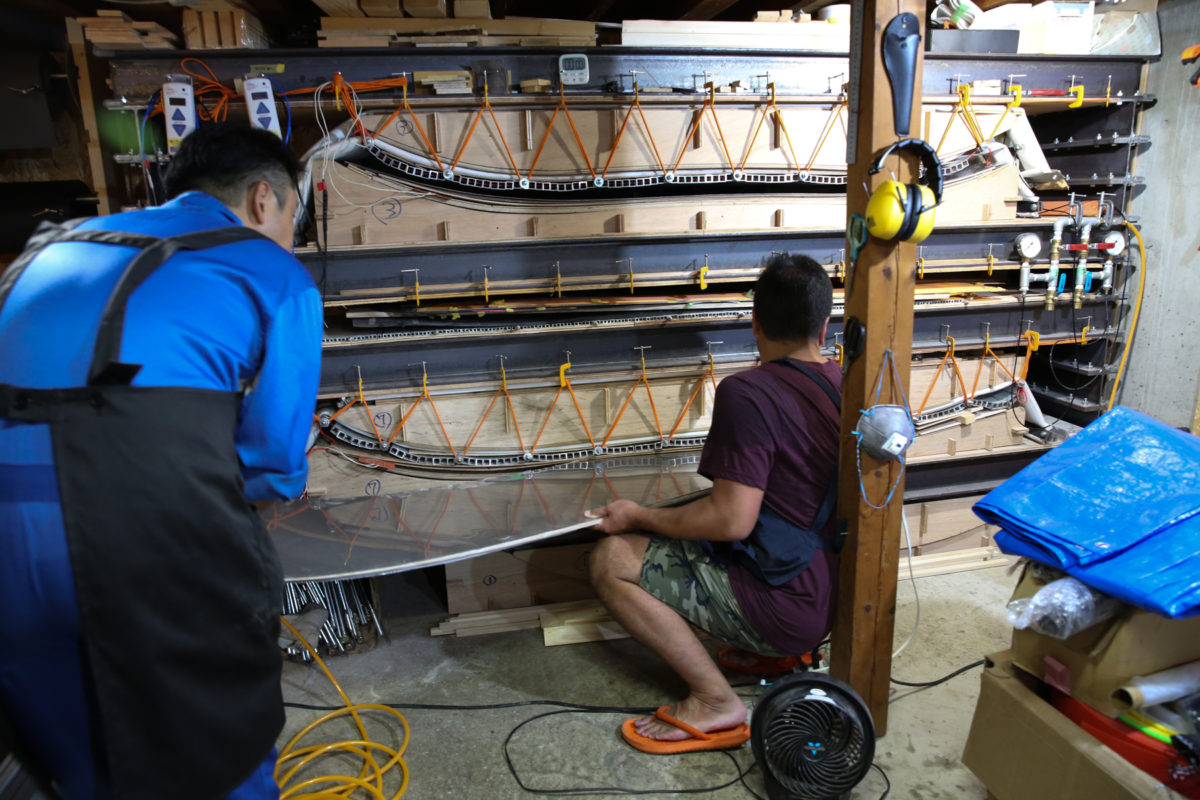
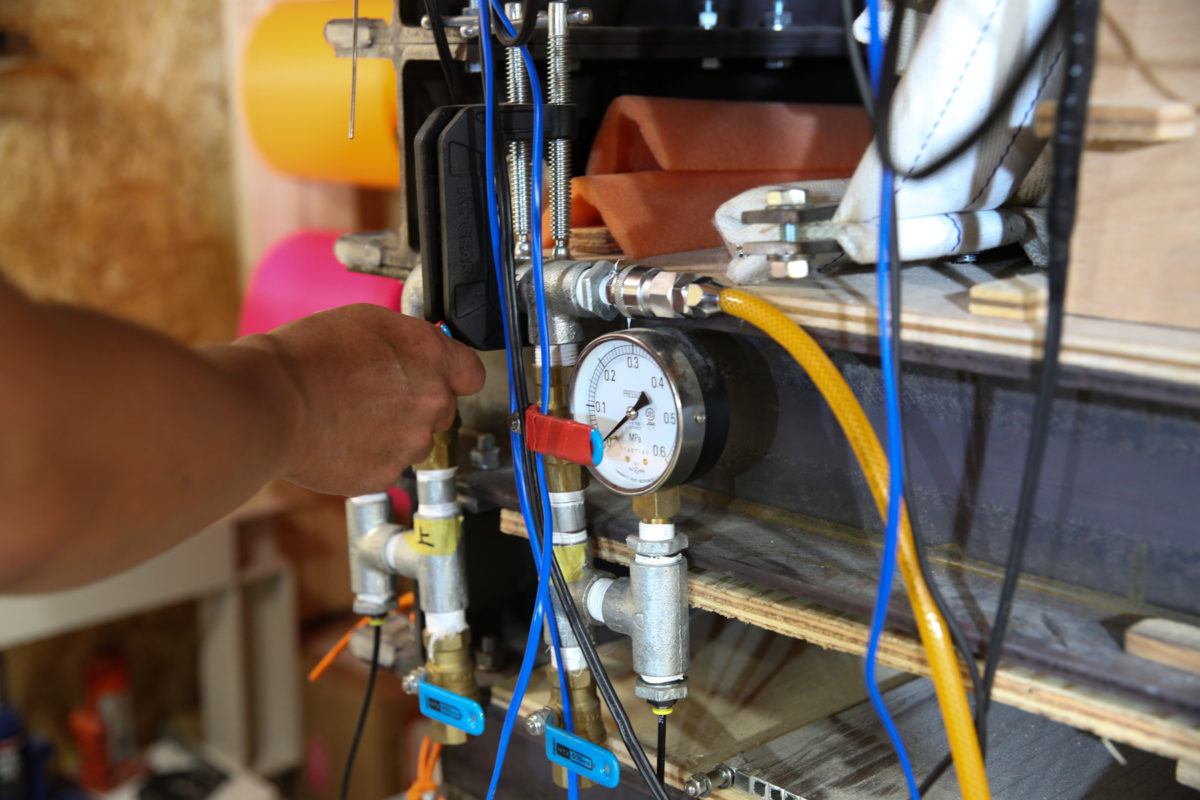
Sæt det i en presse og påfør et samlet tryk på 4 atmosfærer og varme på 80 grader for at fiksere det i cirka 1 time. Pressearbejdet går ud på at lime alle materialer sammen og skabe formen på camber rockeren.
Kun én ski i verden er endelig afsløret
Og dette er hvad der kom ud efter afkøling i en time.
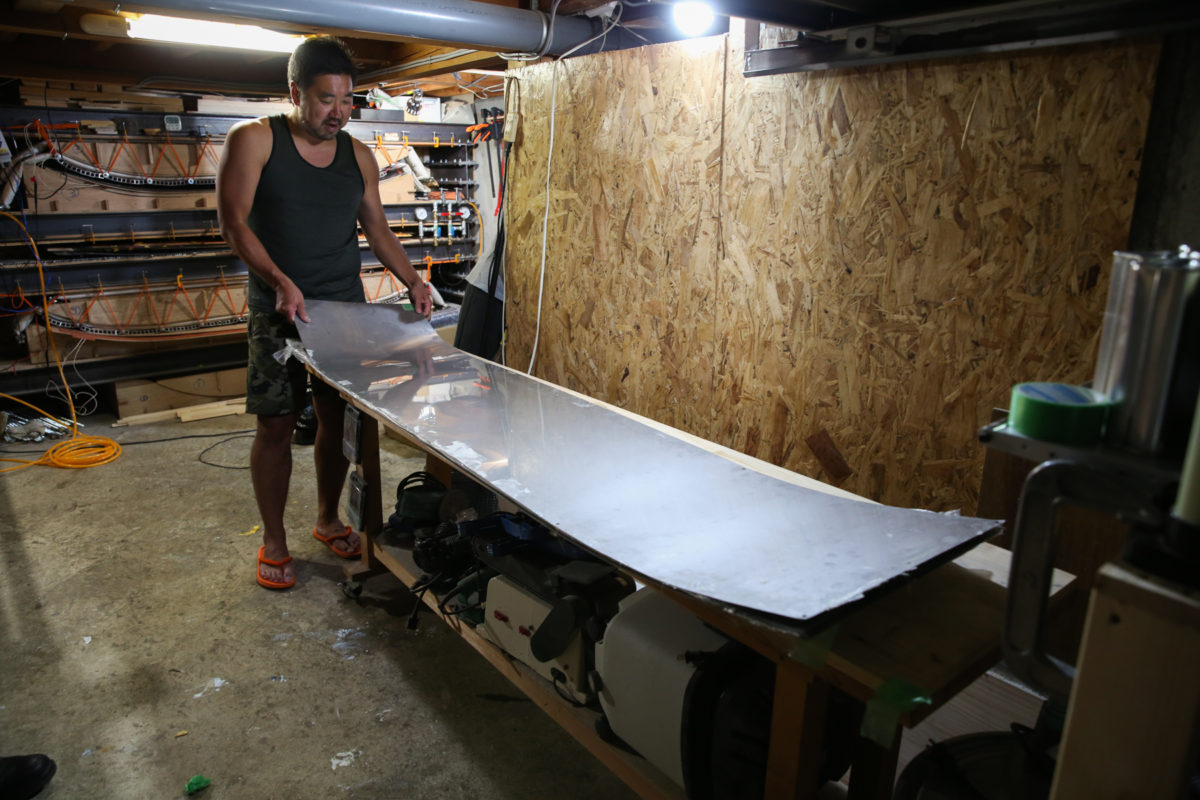
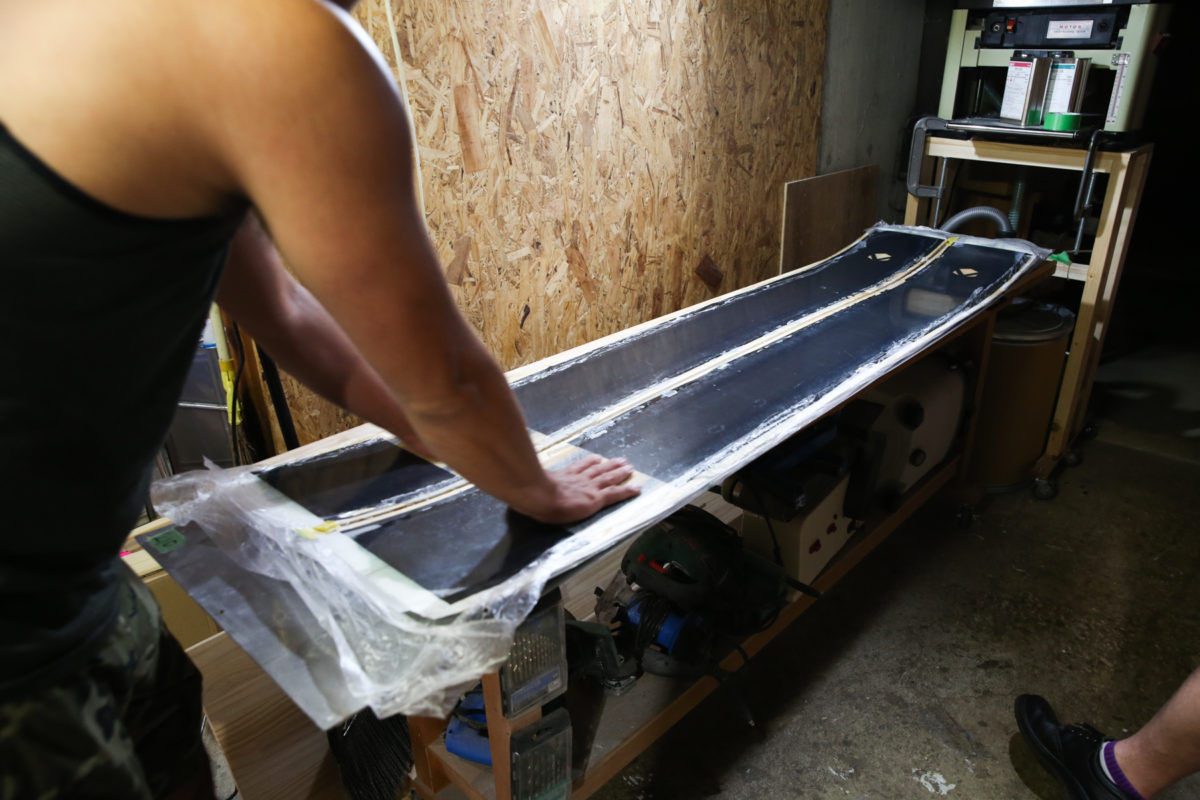
Endelig kom vi tæt på brættets form. På dette tidspunkt er den 90 % færdig. Skær derefter skiens form ud langs kanten.
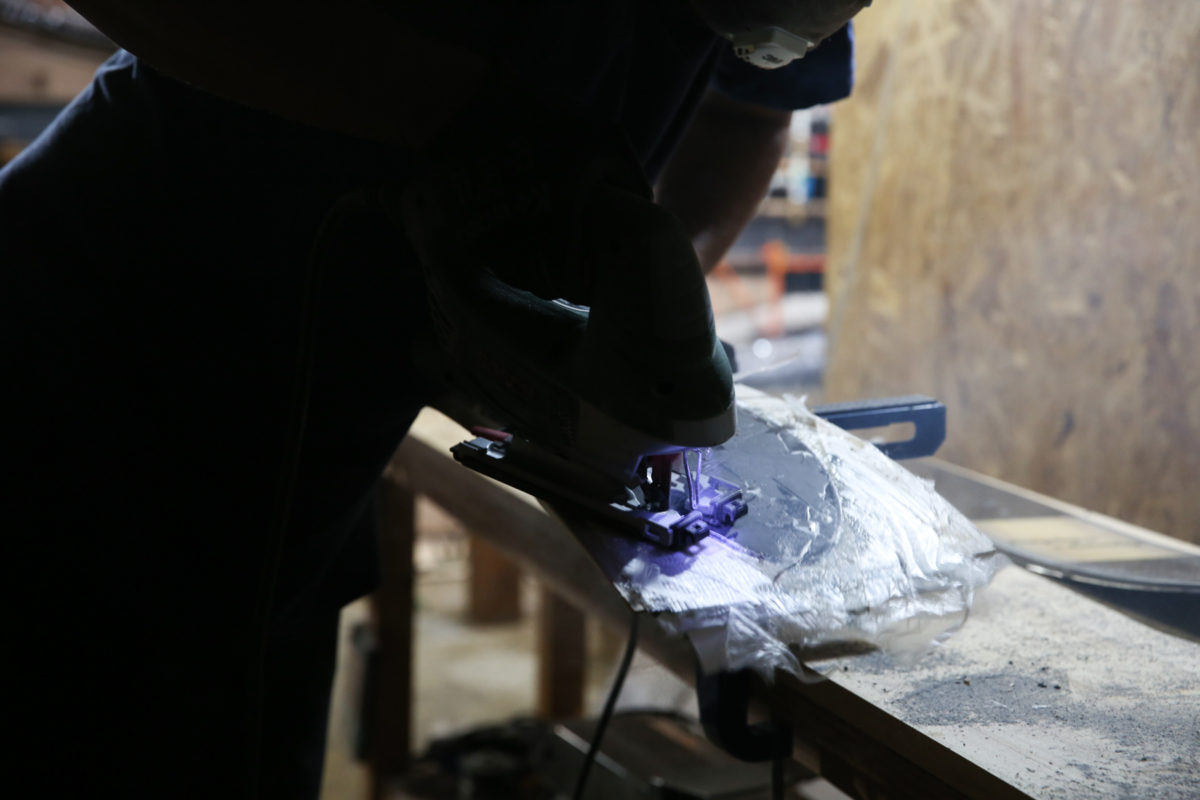
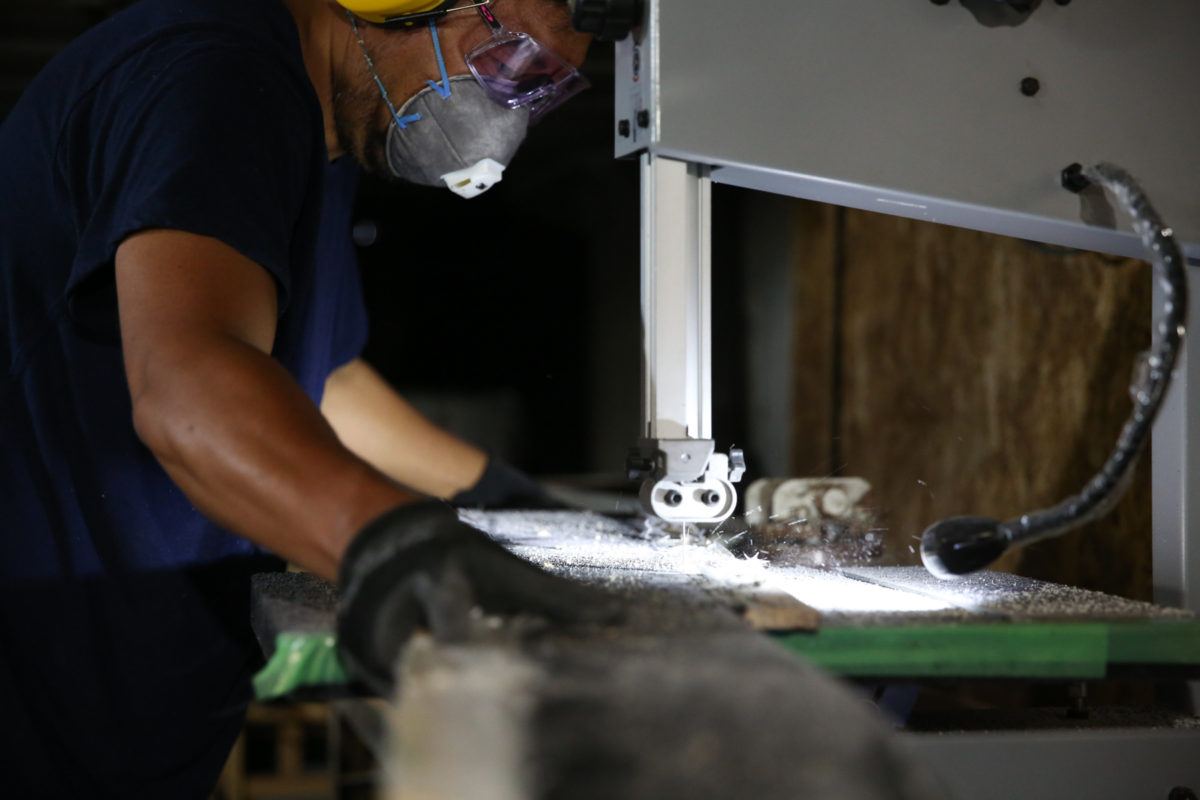
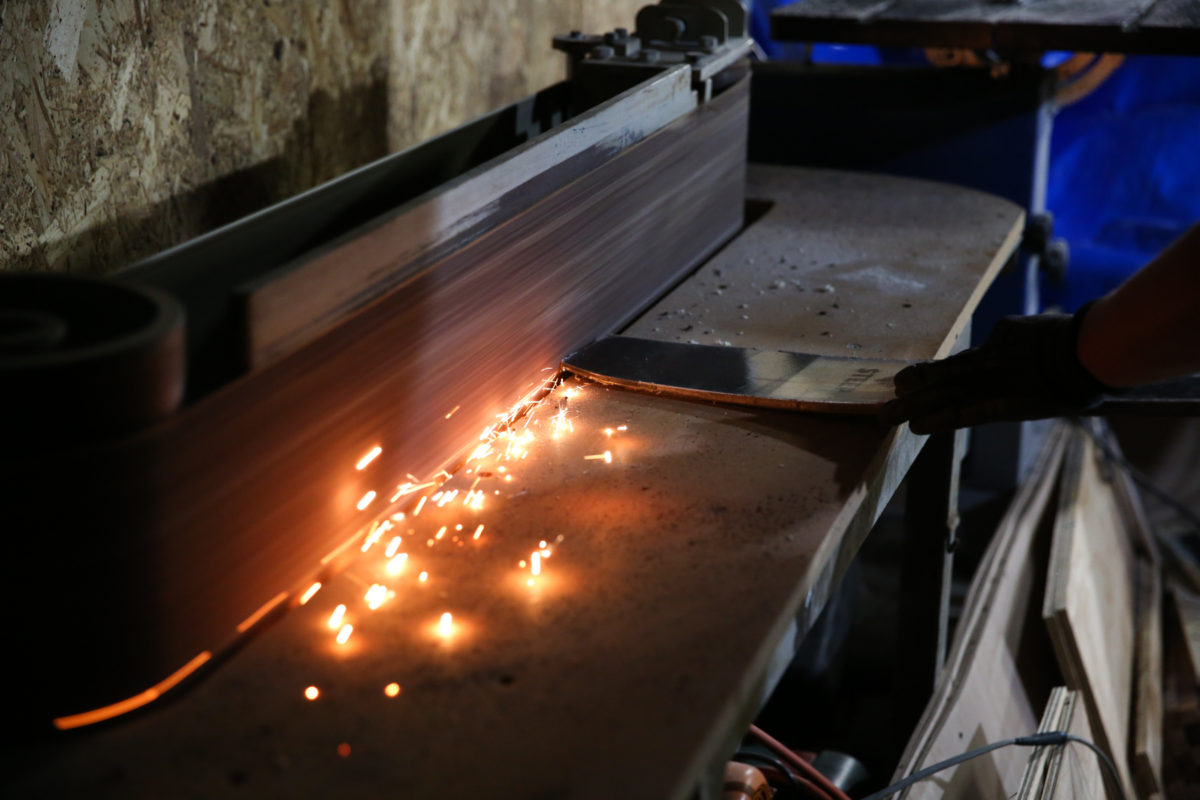
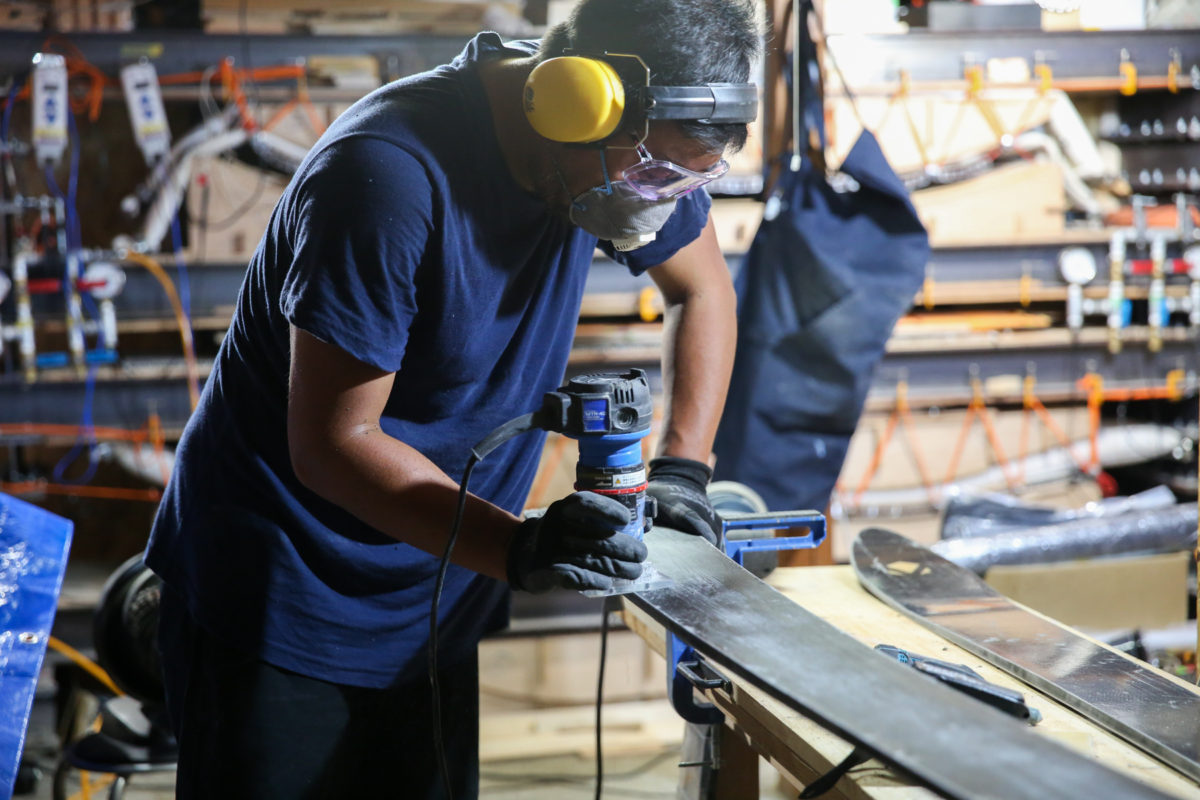
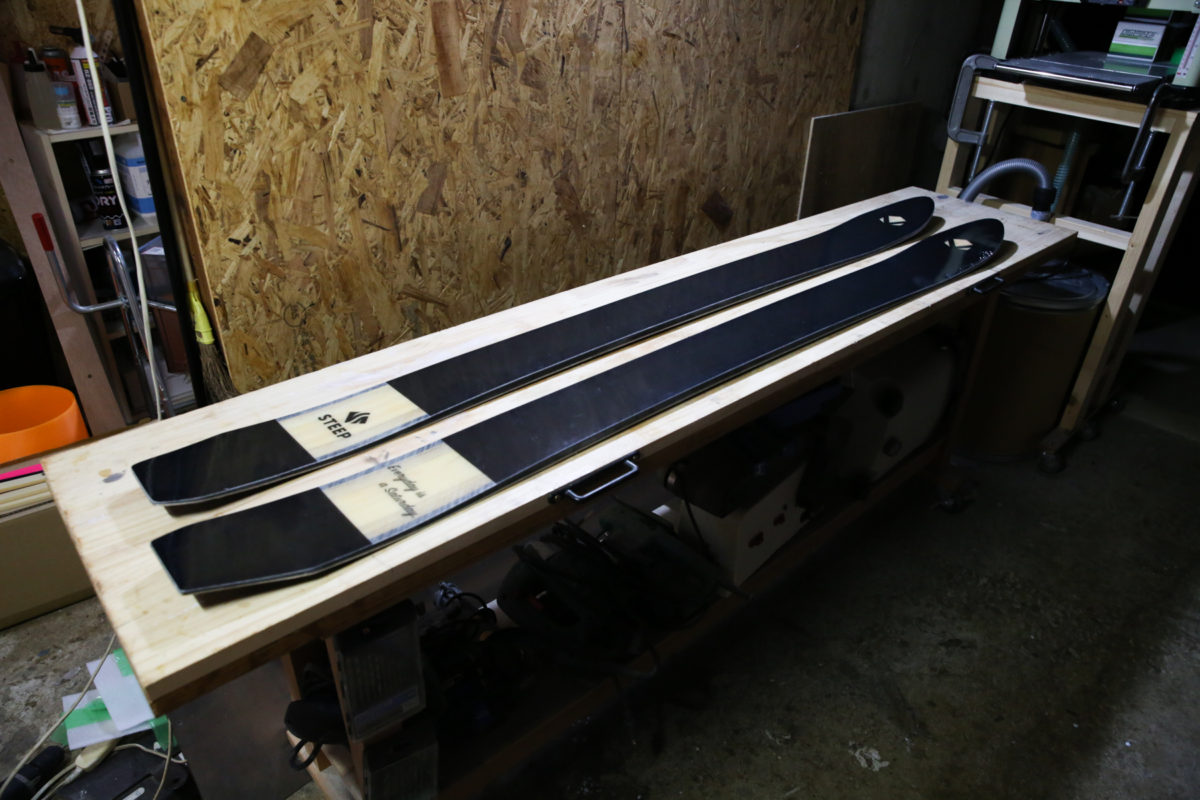
Dette er mit eneste bord i verden indtil videre. Da der er en skabelon, er kopiering selvfølgelig også muligt. Du kan lave det et vilkårligt antal gange. Det opfylder naturligvis også JIS-standarder, så det er korrekt anerkendt som et produkt.
Da jeg faktisk lavede den og så den, var den ægte vare meget sejere end det, jeg havde tegnet i mit hoved.
Jo mere du ser på det, jo mere sejt er det. Formen og grafikken er så cool, at det får mig til at ryste, når jeg tror, at det er det eneste bræt i verden. Fordi jeg har designet det selv, ender jeg med at se på det med mørke briller.
Da pladen stadig er blød, når den er varm efter presning, ser det ud til, at hårdheden vil falde til ro efter cirka en uge.
I den nuværende situation lavede jeg brættet, mens jeg tænkte, at det ville være rart med et blødt udseende, men da jeg lagde vægt på det og bøjede det, gav det indtryk af, at det var lidt for blødt. Hvis dette bliver lidt mere roligt og blødt efter din smag, er det et godt brev.
Derefter skal du faktisk køre på sneen og teste kørekomforten.
Selvom det kun er september, kan jeg ikke vente til vinteren kommer. Jeg vil helt sikkert bære dette board, når skisportsstedet åbner i begyndelsen af november.
Jeg kan ikke lade være med at blive ved med at svæve...
Nå, der er en bekymring, som jeg indså efter faktisk at have lavet bestyrelsen.
Det er mængden af affald.
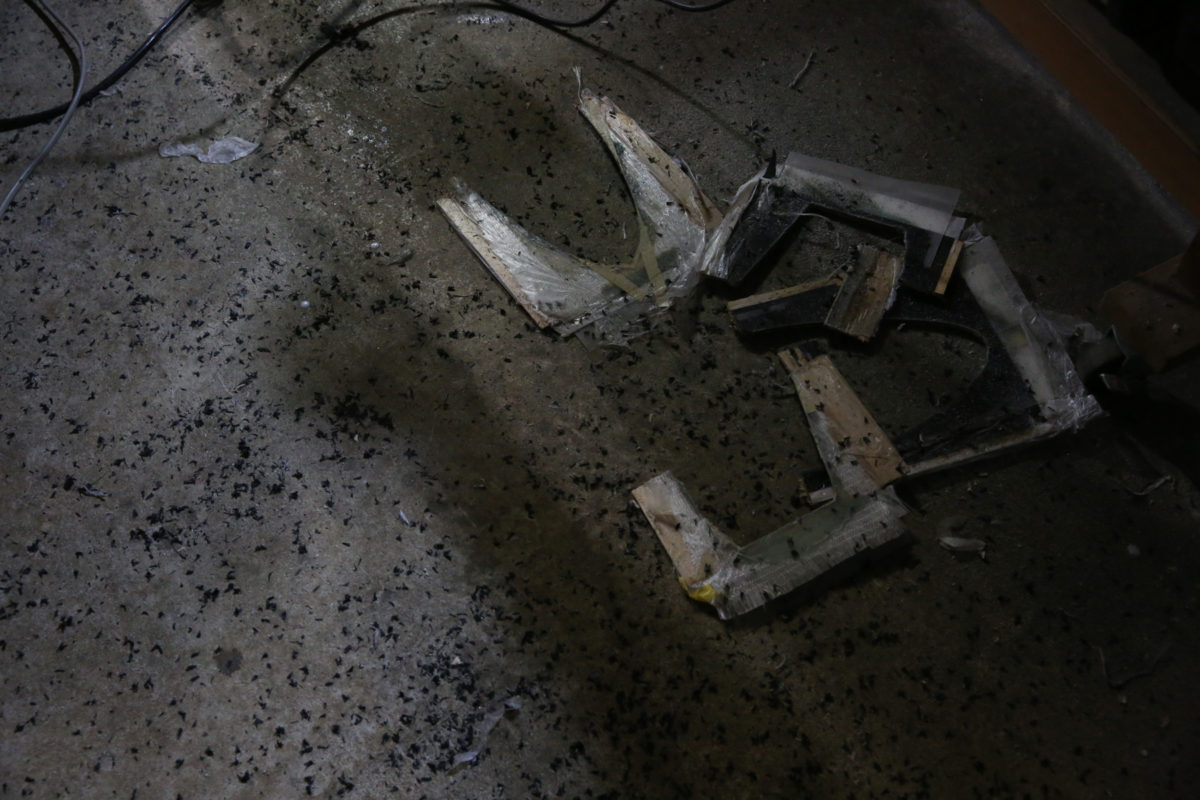
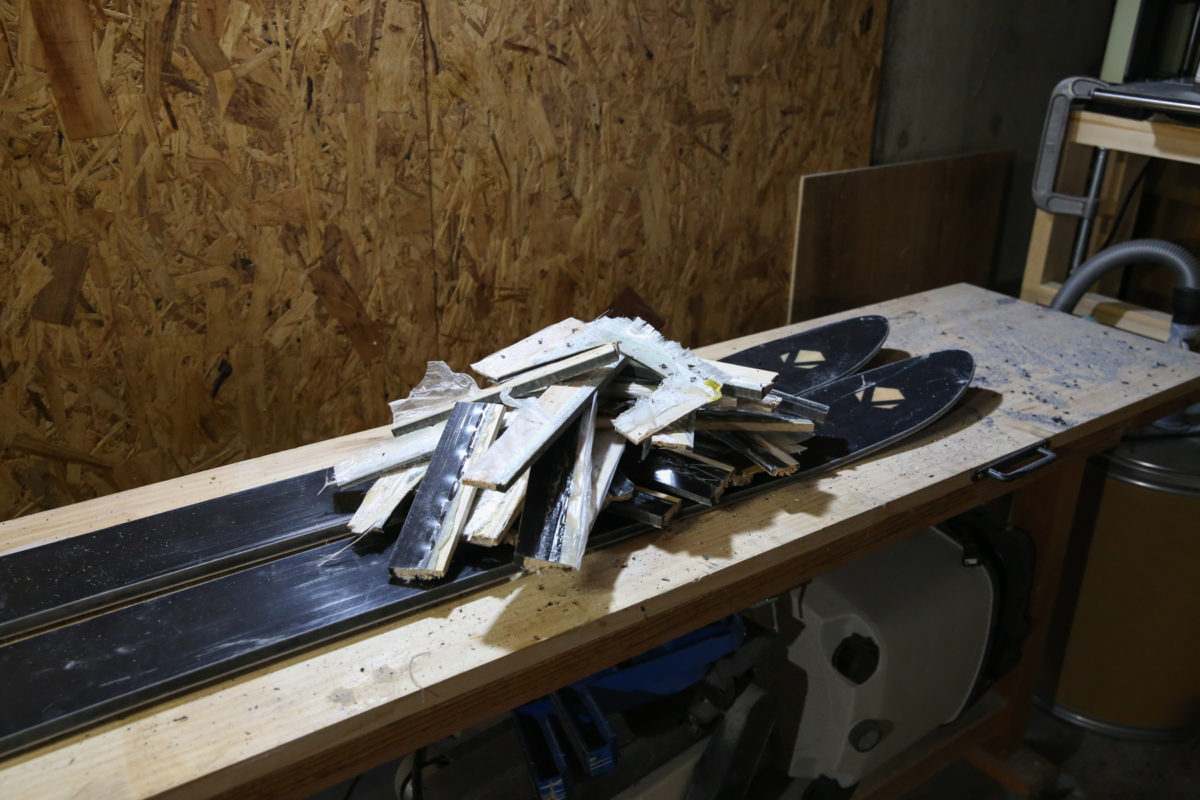
Ovenstående billede er kun en del af det affald, der kom ud i skæreprocessen.
For os, der får lov til at lege i naturen, kan vi ikke bare tage en masse affald ud og glide på pudderet uden at give op.
Selv afbrænding af træ som affald kræver som bekendt transport og brændstof til forbrænding, som igen udleder drivhusgasser. Udover træ indeholder det også fine metaller som glasfiber, så det skal bortskaffes som industriaffald.
Mr. Nagai siger selv
: "I fremtiden er dette affaldsproblem en af de ting, vi skal løse
.
I øjeblikket arbejder Voltage Design på at lave smartphone-covers og tilbehør af de træstykker, der produceres, når man producerer boards, men det alene er ikke nok. Han søger konstant efter mere effektive og drastiske løsninger.
Vi har pligt til at vide det. At producere betyder at forbruge på samme tid. Jeg mener ikke at benægte forbrug, men hvad får du til gengæld for dine aktiviteter? I stedet for at overlade al problemløsningen til andre, vil der være adfærd, som kan ændres ved at tænke på, hvad du selv ved.
Denne gang var det bagsiden af skifremstilling, men hvis dette var et slid eller en handske, ville noget andet blive forbrugt.
At lave sin egen one-of-a-kind ski er en skiløbers største lykke, og samtidig kan man vide, hvad det er for et materiale, hvilken slags struktur og hvilken proces skien er lavet i. Det var en værdifuld erfaring.
Selvfølgelig kan den brede offentlighed også lave deres egne enestående ski og få praktisk erfaring med at arbejde på stedet.
Hvis du har et bræt, du selv har lavet, vil du føle dig mere tilfreds, når du skater. Jeg spekulerer på, om jeg kan ride i lang tid med vedhæftning.
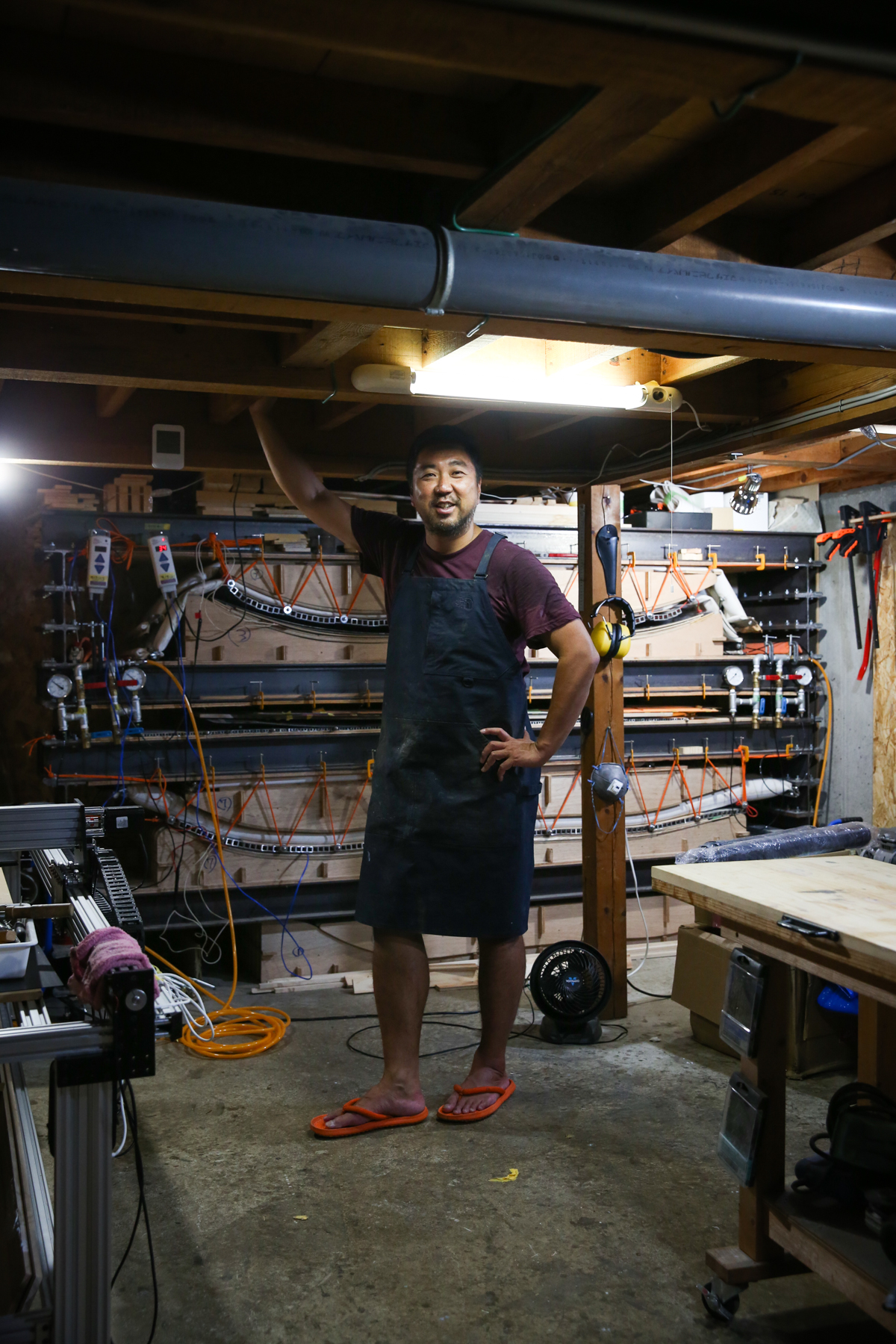
arbejder som bjergguide om vinteren og arbejder hårdt på at lave ski og snowboards dag og nat om sommeren.
Pladeudvikling opdateres dagligt, så tjek Nagais Instagram for detaljer
・Instagram
・Voltage Design HP
Interviewet og skrevet af Daigo Onozuka